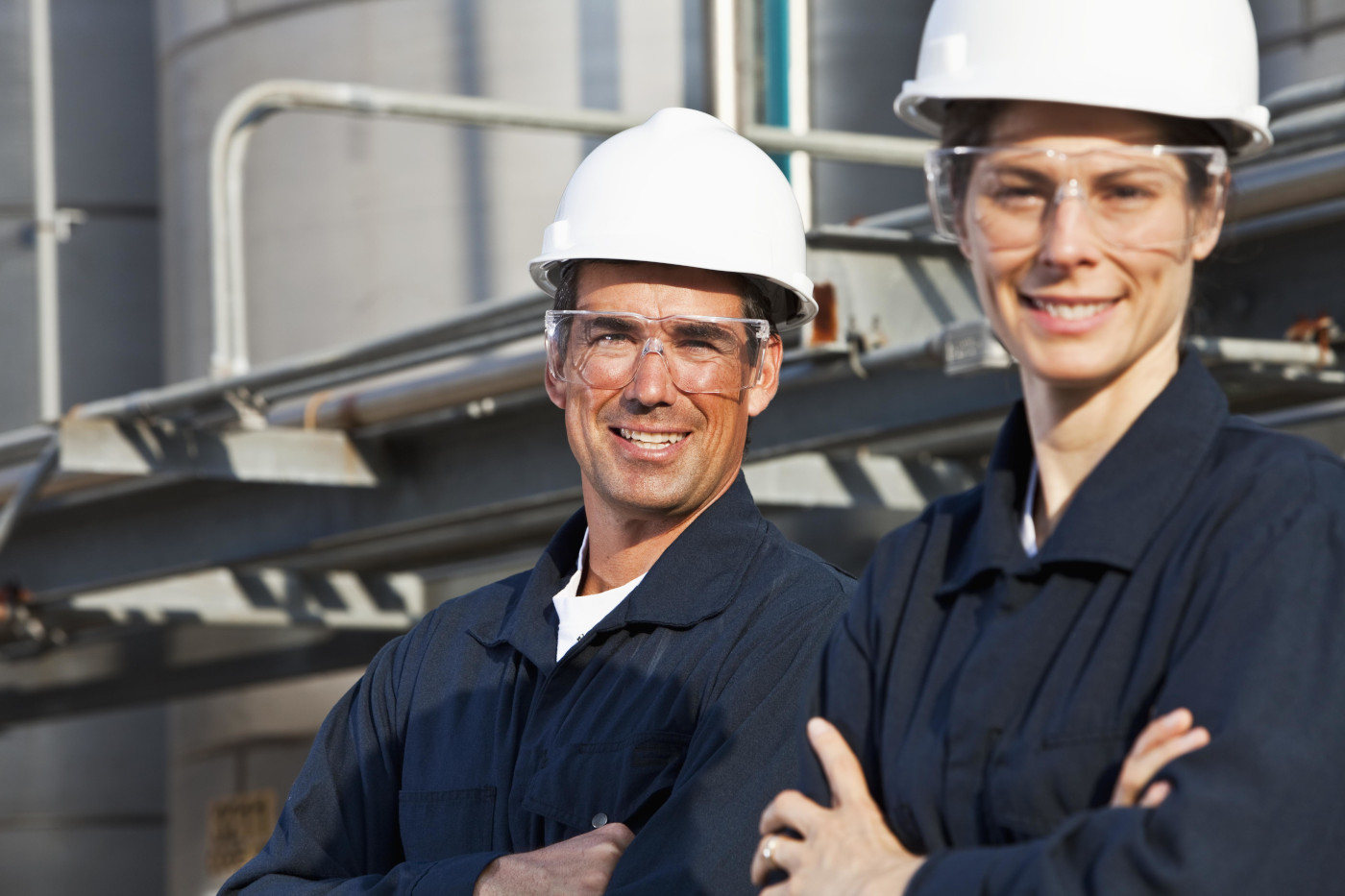
Chemical Engineer's Guide
A Guide for Chemical Engineers in Process, Design and Plant Operations.
Shortcut Distillation
This article describes a widely used shortcut distillation method commonly referred to as the Fenske-Underwood-Gilliland (FUG) method. Read...
Vapor Liquid Vertical Separator
Vapor Liquid separators are one of the most common types of process equipment. This article provides step-by-step procedure for two phase vertical vapor liquid separator design. Read...
Pump Sizing Calculation
Pump is a most common equipment used in a chemical plant to transfer fluid from one location to another. This article shows how to do pump sizing calculation to determine differential head required to be generated by pump based on suction and discharge conditions. Read...
Property Estimation Joback Method
The Joback method is a group contribution method which calculates thermophysical and transport properties as a function of the sum of group parameters. It uses a very simple and easy to assign group scheme. Read...